A blow moulding machine is a machine that is used to produce plastic products with hollow components. The blow molding process involves feeding plastic pellets into the extruder hopper. The plastic pellets are fed into the raw material silos using vacuum pumps. A rotary feeder located at the bottom of the silo controls the rate of feeding into the plastifier. In some cases, compressed air is also used to convey the plastic pellets.
To use a blow moulding machine, operators must understand how the machine works. They should be familiar with the different functions of the machine and how to adjust the mandrel. The machines also have controls for making adjustments. Once the mold has been set, the operators will use handtools to adjust the mandrel to create the desired shape. The machine should also have a pre-pin stand and a parison spreader.
When it comes to choosing a blow moulding machine, you need to determine the type of plastic you will be moulding. The best machines will be able to accommodate a variety of different types of material. PET plastic bottles are widely used. An automatic machine that uses an infrared oven will produce high-quality plastic products. A semi-automatic blow moulding machine is also highly recommended. If you are looking for a fully automatic machine, you may want to opt for a fully automatic model.
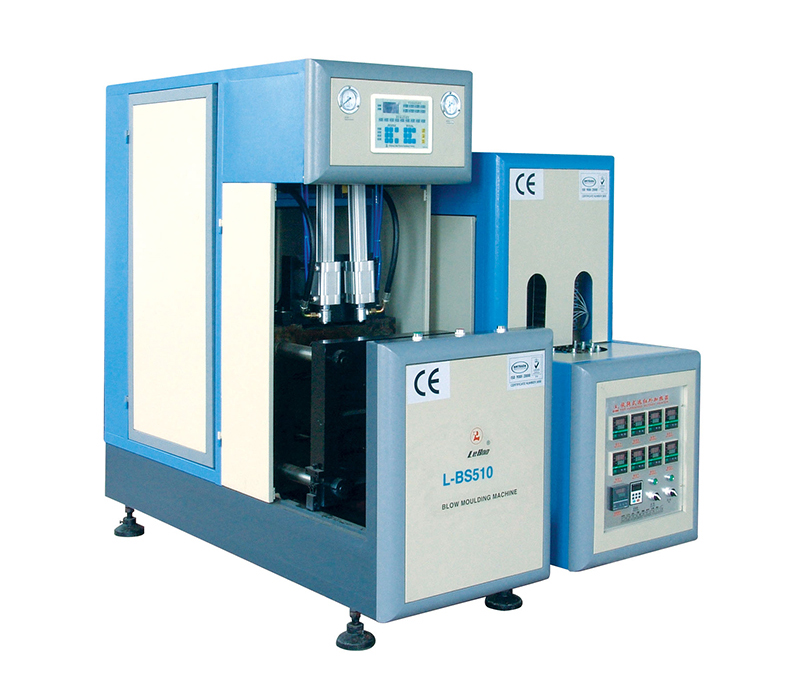
There are several different types of blow moulding machines available. You may want to choose a semi-automatic machine. These machines can produce up to 800 bottles per hour. In addition to the basic types of blow moulding machines, some models are equipped with the most advanced technologies. If you're looking for an automatic blow moulding machine, the UPF-5 is an excellent choice. It features a touch screen and is compatible with CIS countries standards.
Before buying a blow moulding machine, you should determine the size of the parison you'll use. Measure the length of the parison from the face of the tooling mandrel to the bottom of the mold. Make sure to factor in the extra length for prepinching and a parison spreader. You should also know the layflat of the parison before you buy it. You should check its layflat before you buy it.
You should first estimate the length of the parison before you start the blow moulding process. You must take measurements from the face of the tooling mandrel to the top of the mold, and you should also measure the length below the bottom of the mold. Injection blow moulding is the most popular type of this type, while the stretch blow molding is the only one that requires stretching prior to inflation. Injection and stretch blow moulding machines are similar, but they use different types of die heads.