This cuts down on wear on spindle bearings, guides and ball screws. Blow molding machine high-speed cutting and axial milling is also an excellent combination, it is low impact on the spindle bearings, using this approach can use longer overhanging tools with little risk of oscillation. High output rate cutting of small-scale parts, such as roughing, semi-finishing and finishing, has excellent economy when the total material removal rate is relatively low. High-speed cutting of hollow blow molding machine can be achieved in the usual finishing high yield, can achieve excellent appearance quality. The surface quality is often lower than Ra 0.2 um. The choice of high-speed cutting makes it possible to cut thin-walled parts. Using high speed cutting, the tool eating time is short, and the impact and twist are reduced. The accuracy of the mold is improved, and the assembly is simple and faster.
No matter what kind of person and technology, you can get the appearance pattern and accuracy of CAM/CNC production. If a little more time is spent on cutting, the time-consuming manual polishing work can be significantly reduced. Some processes, such as hardening, electrolytic machining and EDM, can often be reduced by as much as 60-100%. This reduces capital costs and simplifies logistical supplies. Blow molding machine with cutting instead of EDM (electric discharge machining), mold life and quality is also improved. With high speed cutting, CAD/CAM can be used to quickly change the depiction, especially if new electrodes are not required. One of the primary objectives of high speed cutting is to reduce production costs through high throughput rates. Blow molding machines are primarily used in finishing processes, often for hardened mold steels. Another approach is to improve overall competitiveness by reducing production time and lead time.
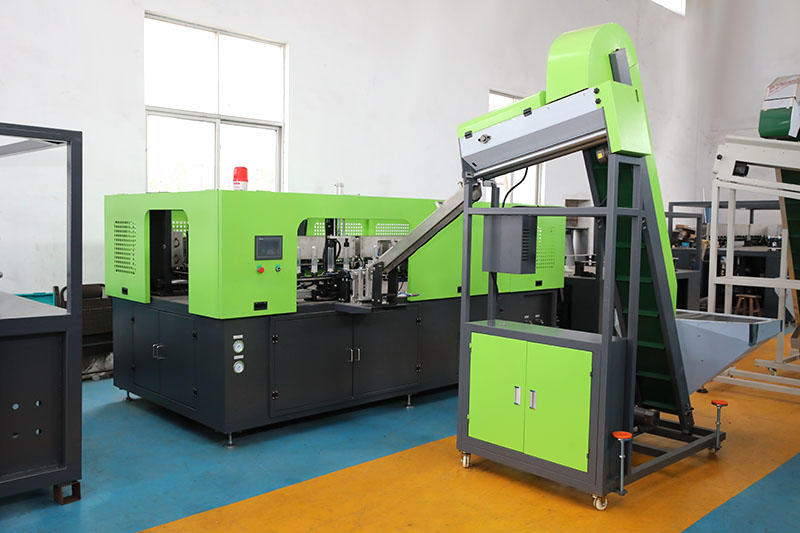