Moog has been at the forefront of blow molding technology since the industry was in its infancy. They provide hydraulic servovalves, machine controllers, and parison control systems, which help machine builders overcome the technical challenges of power and velocity while reducing noise and vibration. Moog solutions deliver cleaner operation, maximum clamp force, and less floor space than competitive models. These blow molding machines are ideal for high-volume production.
A Blow molding machine makes hollow plastic parts by forming a parison. The shape and quantity of parisons are determined by the size of the extrusion head and die tooling. For large, heavy parts, a single extrusion head may be used. For smaller parts, multiple extrusion heads are used. In either case, the plastic is forced through a mold at high pressure, bending the parison into its desired shape and depositing it on the inside.
A Blow molding machine's head section is the next section after the extruder. It includes a die and a mandrel that form a parison, while a screw or ram applies pressure to the molten resin. This part is then ejected from the mold by means of a hollow tube. The finished item then emerges from the cavity of the blowing mold. It's crucial to consider all of these factors when choosing a blow molding machine.
The plastic resin feed is the first step in the blow molding process. The plastic pellets are conveyed from big bags into raw material silos. A rotary feeder on the bottom of the silo controls the rate of feeding. Another option is a vacuum conveyer. If a vacuum conveying machine is not possible, a vacuum can be used. Regardless of the method used, it's critical to understand what happens at every step.
The history of the blow molding process is fascinating. The technology began in the 1st century BC in Syria, and was greatly improved in Egypt during the 1700s. The technology has evolved since then and the industry has grown exponentially. Despite the early days, the process is still a modern manufacturing process. With the rise of plastic containers, blow molding technology has become a staple of the plastics industry. Its benefits are numerous.
Despite these challenges, the Blow molding industry has been booming ever since its introduction. In the 1970s, the United States' soft drink industry saw a rapid rise in the number of its blown products, and continues to grow. The technology has a wide variety of applications, from plastic bottles to automotive parts. A blow molding machine feeds plastic pellets into a screw or hopper. Then, the pellets are heated and extruded into the molds.
One of the most important differences between a blow molding machine and an injection machine is the method of forming the parts. The injection blow molding machine is based on an extruder barrel and a screw assembly. Compressed air is blown into the preform through the opening of the core rod. The finished part is then stripped of the core rod. A leak-testing process is usually performed before it is released from the blow mold.
Blow molding machines are typically used to make hollow parts and plastic products. They feature low tool and die costs and a high rate of throughput. The disadvantages of using a blow molding machine are that it can't produce complex geometric shapes and is limited to producing hollow parts. Further, they're not ideal for producing parts with very high strength. As the process becomes more complex, more advanced technology is required for better accuracy. Ultimately, though, the advantages of this technology are worth the investment.
To determine whether you need to purchase a blow molding machine, you need to consider the final weight of the plastic shot and its mass. This measurement will give you an idea of how much plastic you'll need. Depending on the size of your product, a blow molding machine will depend on the weight of the plastic shot used in the mold. There are two types of blow molding machines: one for a small business and one for an industrial-scale manufacturer.
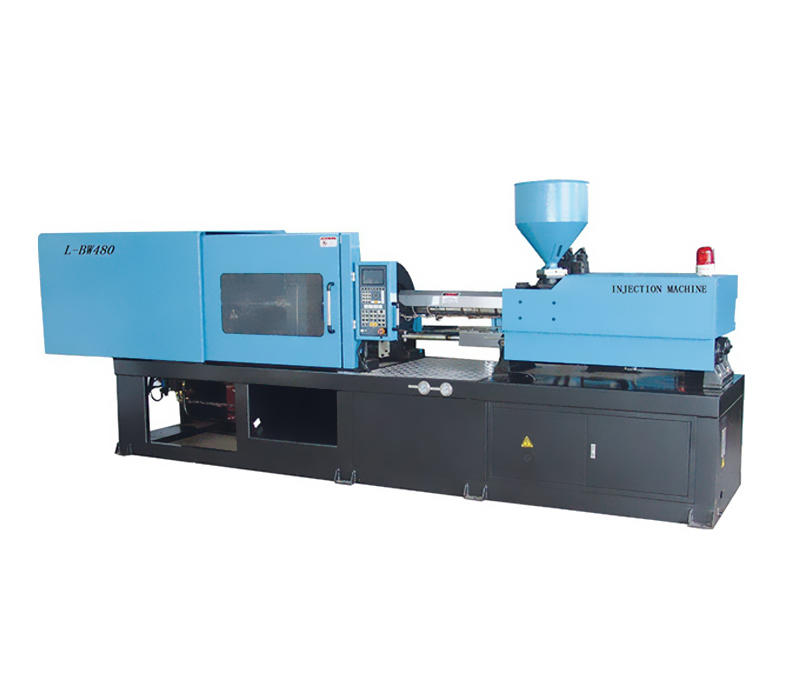