What Xiaobian wants to share with you today are the solutions and key points of operation for common faults of blow molding machines. In fact, the effective measure to solve the failure of the blow molding machine is to have a detailed understanding of the blow molding machine before using it. Understand the information of the electromechanical engineering sub-circuits of the blow molding machine; understand the hydraulic system of the blow molding machine: the stable work of the blow molding machine cannot be separated from the cooperation of the hydraulic system. What we need to know is: the adjustment method and adjustment value of the hydraulic system; static and dynamic Proportional valve current and corresponding pump pressure; understand the integration of mechanical and electrical engineering; I have also shared with you some pre-startup preparations, operation methods and common faults of the blow molding machine. The two points shared here are mainly for further content .
All in all, the preparation before using the blow molding machine is very important, whether it is theoretical preparation or practical preparation. Common operating points of blow molding machine:
1. In order to reduce the self-weight sagging of the parison, under the permitted conditions, the extrusion rate of the parison is accelerated and the waiting time of the mold is reduced;
2. In the production process, the molding cycle should be shortened as much as possible on the premise of ensuring that the product is fully cooled;
3. The inflation pressure should be satisfied during operation, and the air blowing rate should be fast;
4. Control the temperature and speed of the extruder, which is to ensure the quality of the parison and the quality of the product;
5. When the machine is running, ensure that the parison is fully exhausted when the parison is inflated.
6. It is necessary to understand the molding and processing performance of plastic raw materials, so as to adjust the corresponding equipment processing parameters and make better use of the advantages of the material itself;
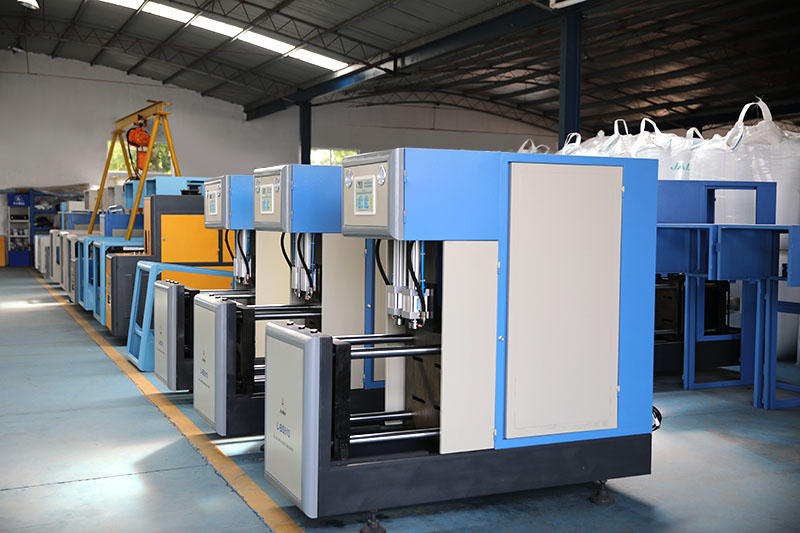